Supporting Sustainable Procurement In The Construction Industry
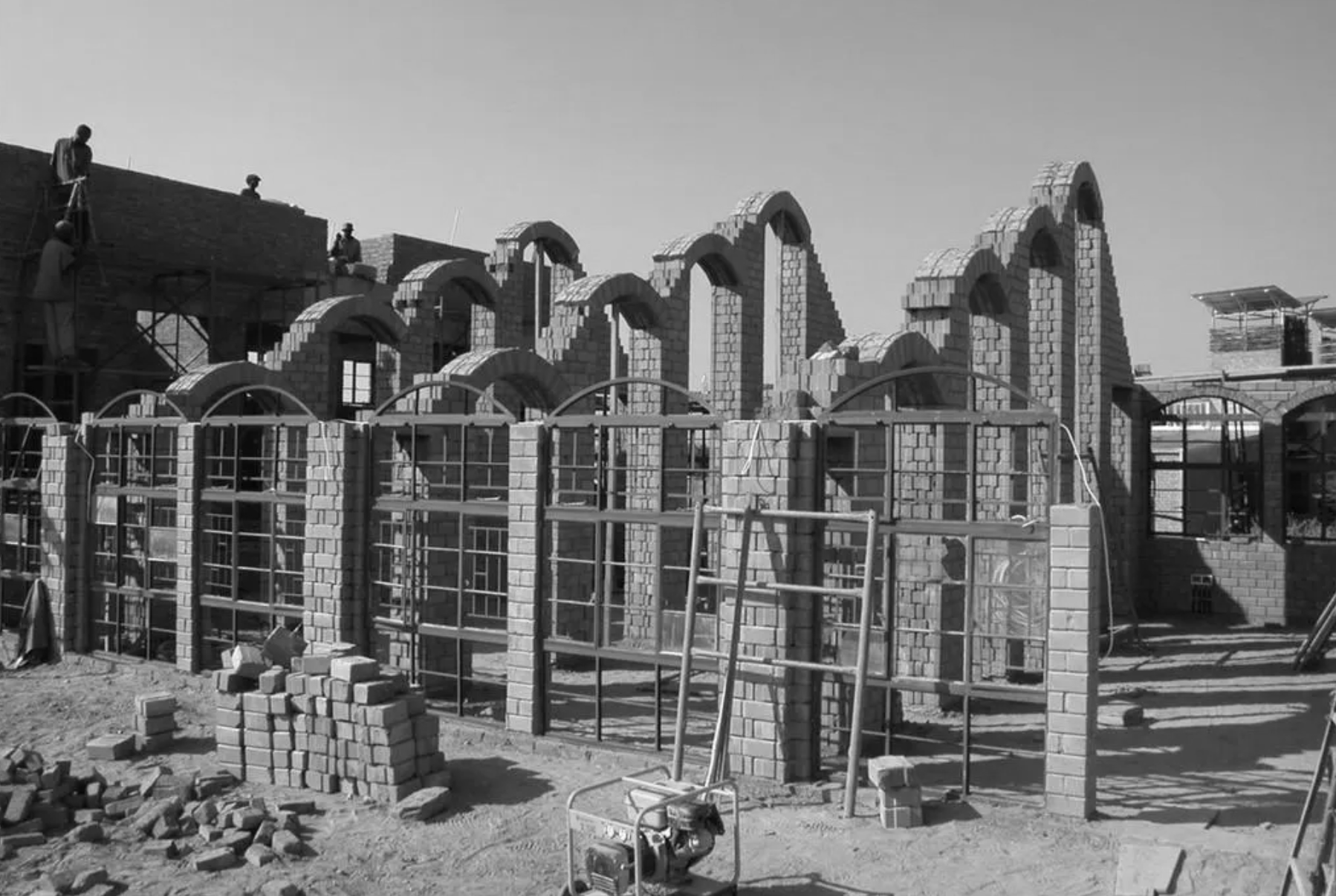
Construction projects are usually long and complex, involving the participation of different stakeholders throughout the different project stages. There are certain factors that are key to determine the sustainability of a project, and the monitoring of these factors necessarily entails the collection of relevant data variables throughout the procurement process.
Define your needs and understand market capability
The following approaches promote data sharing and collaborative approaches in procurement. Applying these will help you to gather relevant information regarding how to best design the procurement process according to your needs, and according to market capability.
Early engagement with the supplier market in the construction sector can be key for collecting the necessary data to define the design brief and specifications of the project. See this section for more information on market engagement methods.
Integrating suppliers from a construction project’s life-cycle as early as possible in the procurement process can help to set relevant sustainability targets and ensure commitment. This can be achieved by promoting collaborative procurement mechanisms that involve Early Supply Integration (ESI) . See the next section on “Selecting the best procurement practices” for more information on these.
Creating a hub where data from finalized infrastructure projects is stored can facilitate investment decisions on future construction projects. This data will help to promote continuous improvement regarding project brief definitions, ensuring better use of resources and facilitating knowledge sharing regarding sustainability practices
Select the best procurement practices
The following procedures can constitute the characteristics of a single procurement procedure, or individual characteristics of certain procurement processes.
Outcomes-based and performance-based approaches are often used in construction for maintenance and operation contracts. See this section for more information.
Ceiling costs in construction projects are calculated according to the identification and clear definition of project targets. These details are shared with supply teams, who have to come up with a plan that meets the defined targets.
This approach requires suppliers to collaborate and openly share the information that will allow them to present a successful project proposal. A price ceiling will also encourage suppliers to evaluate the real need of resources, which will minimize the risk of overestimating material need and, in turn, minimize waste generation.
Finally, if project targets include environmental considerations, this approach also leaves room for suppliers to come up with innovative ways to reach these targets without exceeding the price.
Two stage procurement procedures in the construction sector usually involve a first stage where a contractor, or a limited number of bidders, are selected based on specific criteria, which can include previous experiences, capabilities, or project proposals. The work carried out by this team is used as the basis to select the final project team during the second stage.
This approach can often be seen in design and construction projects, where the design of the building is determined by the input of those selected during the first stage, ensuring better market fit and, if it is an integrated team, a life cycle approach.
Two stage procurement procedures allow for ongoing dialogue and open disclosure of information between suppliers and procurement practitioners. This can be especially useful for negotiating ways to reach sustainability targets in construction projects. See this section for more information.
An integrated team can include contractors, subcontractors and suppliers of a single project stage (i.e. deconstruction, design, etc.), or/and stakeholders from the whole project’s life cycle (i.e. design, construction and maintenance or operation).
If an integrated team is put together early on in the procurement process, it will facilitate coordination throughout the project and promote data sharing, which will minimize risks, improve resource estimation, and ensure that sustainability targets permeate through the whole project life-cycle.
Third-party insurance policies are sometimes included in procurement processes to cover risks associated with delivery of a construction project. The insurance packages all insurance policies from stakeholders, including the procuring agency, main contractor, and all suppliers. The outturn cost above the target cost plus pain-share is insured.
Having an integrated third-party insurance policy can help to promote supply-chain integration and collaboration. By covering project outcomes rather than individual liabilities, this policy can help to remove blame culture amongst suppliers. Furthermore, in order to secure the insurance in the first place, the proposal presented by the team will have to be detailed and credible. This requires careful project planning and coordination amongst all team members.
Data about all aspects of the project will have to be openly shared with all stakeholders, including the procurer and the insurance company. Risk minimisation and better evaluation of resource needs will be a side effect of this process, which will contribute to minimize the project’s environmental impact.
Resources
Guidance on using two-stage procurement processes in construction projects:
- User Guide for Procurement of Plant Design, Supply, and Installation. 2021. Asian Development Bank (ADB)
- Procurement of Works: Two-Stage Open Tendering Procedure. 2019. European Bank for Reconstruction and Development (EBRD)
- User’s Guide for the SBD for Procurement of Plant Design, Supply, and Installation. 2018. African Development Bank (AfDB)
Guidance on including early supply integration in construction projects at the design stage:
Step-by-step guidance on how to carry out an Integrative Design Process (IDP), with links to relevant guidance and tools at each step.
Case study
The construction of The Habitat Research and Development Centre (HRDC) in Namibia was procured using a two-stage tender. The two bidders chosen after the first stage, and their Quantity Surveyors, drafted the Bill of Quantities (BOQ) that would be included in the second stage.
Openly sharing information during the time between the two stages of the tender allowed the experienced team to come up with sustainable materials and methods to include in the BOQ, all of which they based on available local resources.
Case study
In 2006, Scotland’s Forth Road Bridge showed in signs of significant deterioration. After a review, it was decided that a new bridge would be built next to the existing one. Due to the complexity of the project, Transport Scotland decided to engage with the market in order to gain knowledge and assess the procurement plan. This was done by organizing an Industry Day with top contractors, where a Questionnaire was distributed. Following this, bilateral conversations were established with suppliers to come up with the best possible plan. These activities shaped many aspects of the procurement procedure, including contract details and the employer’s requirements.
If you’d like to discuss your government procurement data needs, find out more about our data API, or talk to us about our carbon database,get in touch.