Why Is Sustainable Procurement Important For The ICT Sector?
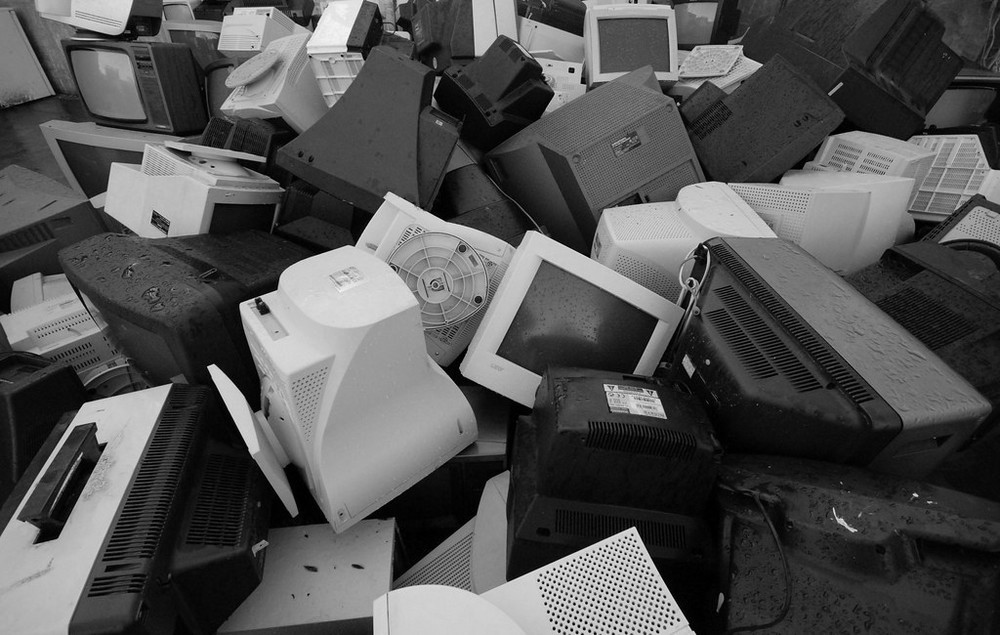
The extraction of raw materials, manufacturing, transportation, use, and disposal of ICT products is associated with a number of environmental, social, and economic externalities.
The extraction and disposal of minerals used in the ICT sector are associated with material toxicity and resource depletion. It is estimated that, although e-waste generated in the ICT sector accounts for only 2% of solid waste streams, it represents 70% of the hazardous waste that ends up in landfill.
The environmental impacts associated with the ICT sector also have a strong impact across the economic and social pillars of sustainability. Material toxicity, for example, can have negative impacts on the health of workers across the supply chain, mainly those involved in mining, smelting, manufacturing, and e-waste handling. Due to the lack of transparency in the ICT supply chain, it is difficult to monitor these activities, which are often also associated with labour rights violations.
Here, we focuses on the purchase of hardware equipment, which mainly includes displays, notebooks, desktops, all-in-one PCs, projectors, headsets, network equipment, data storage devices, servers, printers, and scanners.
1. Identifying relevant regulations
The application of Open SPP when procuring ICT equipment can be guided by the existence of certain compliance frameworks that address some of the sustainability challenges in the sector. These can include:
Ratification of the core eight ILO conventions can help to guide what information can be requested of suppliers regarding labor rights in the supply chains.
Many countries have specific regulations regarding the management of electronic and electrical waste (e-waste). For example, Mexico, which is the third global producer of e-waste, has recently amended their waste management regulatory framework to include specific provisions regarding e-waste management. These regulations often include provisions regarding hazardous waste management (batteries, etc.). This framework can be useful to determine the obligations regarding waste management that should be clearly communicated to the supplier and included on the contract.
Look for existing sustainability standards
Existing sustainability standards, and ecolabels for the ICT sector can help you when deciding what criteria to set during the procurement process. For more information on what ecolabels are, the different types, and how they can be used in procurement see this guide. Below we include some of the key standards developed for this sector.
TCO is an international Type I ecolabel that provides standards for sustainable ICT equipment. This includes criteria for displays, notebooks, tablets, smartphones, desktops, all-in-one PCs, projectors, headsets, network equipment, data storage, and servers.
Energy Star is a Type I-like ecolabel which sets a maximum level of energy consumption for electric appliances. The Energy Star rating or certification can help you identify products which are held to a higher energy use and emissions standard.
Aside from these two, other ecolabels which cover ICT products include the Taiwan Green Mark, the Korea Eco Label, the Blue Angel ecolabel for printers. The EU has also developed sustainability criteria for the procurement of “Imaging equipment, consumables and print services” and of “Computers, monitors, tablets and smartphones”.
2. Selecting Your Data
When implementing SPP in specific procurement categories, it is important to understand what factors should be monitored to measure the impact of the contract across the three sustainability pillars.
Recycled content
The use of recycled materials in ICT equipment can contribute to lower its environmental impact. Some of the variables that can be considered are:
One variable that should be considered when procuring ICT equipment is the total % of recycled content.
Ecolabels, such as TCO, measure, specifically, the use of post-consumer recycled plastic (plastic derived from used consumer products, such as bottles, or recycled IT products). It is calculated that plastic represents around 21% of the material content in IT equipment, thus, encouraging the use of a minimum % of plastic derived from used consumer products (post-consumer recycled plastic) can have a positive impact on the environment.
Recycled content in packaging materials should also be monitored. This can include for example ensuring that paper-based packaging is 100% recycled, and complies with the standards set by ecolabels such as Forest Stewardship Council (FSC).
Another variable that can be considered when procuring ICT equipment, particularly printing equipment, is whether 100% recycled paper can be used in the printer. Another variable that can also be used to measure the sustainability of printing equipment can be whether double sided-printing is an integral capability of the equipment and set as default.
Energy efficiency
Energy efficiency is the main variable that will determine the environmental impact of an ICT product during its use life. To measure energy efficiency, Typical Energy Consumption (ETEC) per year should be captured (calculated in kWh). Compliance with Energy Star can be set as technical specification to ensure better energy efficiency, this indicates that the product uses less energy than at least 75% of available products in the market.
Hazardous substances
The use of hazardous substances in ICT equipment can be dangerous for those handling the materials throughout the life-cycle of the product, from manufacturing to waste management. Information can be required from the supplier regarding the efforts to reduce or eliminate the use of these substances.
Repairability, upgradeability and recyclability
Sustainable practices in the ICT sector aim to promote circularity and prolong the use life of existing equipment in order to minimize the environmental impact associated with the manufacturing of new equipment. Repairing, upgrading and recycling existing equipment is one of the main ways to achieve this goal. To measure the repairability, upgradeability and recyclability of ICT equipment, the following variables can be considered:
Most ICT sustainability standards determine that spare parts should be available for a minimum period of 4 years after end of production.
If the manufacturer, brand, or reseller, offers a repair service as part of the contract is another variable that can help to ensure repairability of ICT equipment. It should also be captured whether the expenses associated with this service will be incurred by the public authority or the supplier, and whether this will be for the whole use life of the equipment, which is usually a minimum of 3-4 years. Generally, if repair costs are carried by the supplier, it can be an incentive to design a product that is easier to repair and recycle.
To promote the repairability of ICT equipment, sellers should include a Service Manual with instructions on how to repair the equipment. The TCO Ecolabel includes standards of what information should be included on these manuals. If ICT equipment is designed in a way that facilitates the replaceability of its components, it will not only help to extend use life, but it will also increase the equipment’s recyclability.
Data security
Data security information is a variable that should be captured to ensure that privacy and security have been built into the procured ICT hardware. Page 15 of HP’s sustainable IT purchasing guide provides guidance on data security information that procurers can require of potential vendors and the technology purchased.
End-of-life management
In order to promote the circularity of ICT equipment, it is important to collect information regarding the services the supplier offers at the end of the use life of the equipment. For example, this can be clearly captured whether the supplier can provide a take-back, re-use or recycling service, and whether this service is also available for individual components, such as batteries.
Supply chain information
One of the key issues within the ICT sector is the lack of transparency regarding the supply chain, which is often associated with occupational health and safety violations, and labour rights vulnerabilities. Requesting and capturing the following information from the supplier is an important step towards to promote social sustainability in the ICT sector:
One of the variables that can be captured from a supplier, is whether there is publicly available information regarding the supply chain. This would ideally include all the different companies involved, from mining, to refineries, component producers, manufacturers, etc. This information can be required of the equipment that is the subject matter of the contract.
Suppliers should monitor labor rights through a publicly accessible Code of Conduct or Supplier Policy.
According to TCO standards, this code should be consistent with:
The supplier should also provide information on how this Code of Conduct is transmitted to supply chain (translations, questionnaires, training, etc.), how it is monitored (frequency, identification of countries or suppliers with higher risk, etc.), corrective actions taken, and any collaboration with third parties to monitor compliance with Code of Conduct.
Resources Introducing responsible supply-chain criteria in the procurement process:
The Region Stockholm is one of the European leaders in implementing social criteria for ICT procurement. This resource provides guidance on how this criteria should be introduced and monitored throughout the procurement process.
The RBA has created a framework with a set of Corporate Responsibility Indicators (CSR) that aims to harmonize and simplify the process of supply chain assessment.
Introducing general sustainability criteria in the procurement process:
3. Selecting Your Data
Once the key sustainability variables have been identified, it is important to determine how, and when, these will be collected throughout the procurement process and the duration of the contract.
Request relevant documentation
The information from the previous section will guide decisions on what criteria should be evaluated during the procurement process. To verify the compliance of suppliers with the established criteria, information gathered will include:
- Supplier Code of Conducts or supplier policies.
- Service manuals with maintenance and repairs information.
- Accreditation certificates or awarded ecolabels.
Gather evidence during implementation
Specific social criteria regarding supply chains should be included in the contract clauses to ensure compliance, and encourage continuous improvement towards transparency and labor rights monitoring. To gather the necessary data to monitor compliance with agreed criteria, the following methods can be used:
Questionnaires can be useful to monitor the compliance with supply chain conditions set in the contract by distributing questionnaires to ICT suppliers throughout the duration of the contract. These questionnaires will require information and proof regarding the activities they are carrying out to comply with social criteria set in the contract clauses. The information gathered from the questionnaires can help to assess the need of conducting any further desktop or factory audits.
One way to monitor supply-chain activities is by conducting desktop audits and factory visits. Conducting factory audits can be resource intensive, which is why it can be helpful to collaborate with a third party, such as and NGO.